
Concrete Coatings Workflow Process:
01
Initial Assessment
-
Conduct an on-site evaluation to understand the client’s needs, assess the concrete's condition, and measure the project area.
-
Identify potential challenges, such as cracks, moisture issues, or structural damage.
-
Provide the client with product options, finishes, and a detailed estimate.
02
Surface Preparation
-
Cleaning: Remove dirt, debris, grease, or oil using pressure washing or appropriate cleaning agents.
-
Repairing: Patch cracks and fill joints using epoxy or other fillers to ensure a smooth surface.
-
Grinding/Etching: Use diamond grinders or chemical etching to profile the concrete surface, ensuring optimal adhesion for the coating.
-
Dust Removal: Vacuum the area thoroughly to eliminate all dust and particles.
03
Priming
-
Apply a high-quality primer to enhance adhesion between the concrete and the coating.
-
Ensure even application and allow proper curing time as per product specifications.
04
Base Coat Application
-
Mix and apply the base coat evenly using a roller or squeegee.
-
Allow the base coat to cure according to the manufacturer’s recommendations.
05
Decorative Layer (Optional)
-
If using flakes, metallics, or other decorative elements, broadcast them evenly across the wet base coat.
-
Scrape and vacuum excess flakes after curing to prepare for the topcoat.
06
Topcoat Application
-
Apply a durable, UV-resistant topcoat for protection and a polished finish.
-
Use tools like rollers or sprayers for even coverage.
-
Allow sufficient curing time based on the environmental conditions and product requirements.
07
Quality Inspection
-
Inspect the finished surface for imperfections, uneven areas, or missed spots.
-
Address any issues promptly.
08
Final Walkthrough
-
Conduct a walkthrough with the client to review the completed project.
-
Provide maintenance tips and any warranty information.
09
Cleanup
-
Remove all equipment, materials, and debris from the site.
-
Leave the area clean and ready for use after curing.
10
Follow-Up
-
Check in with the client post-installation to ensure satisfaction and address any questions.
Custom Cabinets Workflow Process:
This workflow ensures the highest quality in designing and installing custom cabinets for garages, laundry rooms, and closets.
01
Initial Consultation
-
Client Meeting: Understand the client’s needs, preferences, and style. Discuss space usage, storage goals, and design inspirations.
-
Site Assessment: Visit the location to measure dimensions and assess structural and environmental factors.
02
Design Phase
-
Space Planning: Develop a layout that optimizes functionality and aesthetics for the space.
-
Material Selection: Present options for cabinet materials, finishes, colors, and hardware.
-
3D Rendering: Provide a digital mockup of the proposed design for client review and approval.
03
Quote and Contract
-
Cost Estimation: Offer a detailed quote that includes materials, labor, and installation.
-
Approval: Finalize the design and obtain client approval on budget and timeline.
-
Agreement: Sign a contract outlining the scope of work, payment terms, and warranty details.
04
Material Procurement
-
Order Materials: Source high-quality materials and hardware based on the approved design.
-
Quality Check: Inspect all materials for defects or inconsistencies before use.
05
Manufacturing/Pre-Installation
-
Custom Fabrication: Build cabinets to specification in a workshop or on-site as needed.
-
Finish Application: Apply stains, paints, or protective coatings.
-
Quality Assurance: Inspect cabinets for precision, durability, and alignment to design specs.
06
Installation
-
Site Preparation: Clear the workspace, ensure structural readiness, and protect surrounding areas.
-
Cabinet Installation: Secure cabinets to walls or floor using proper anchoring techniques.
-
Hardware Attachment: Install handles, knobs, and other hardware.
-
Functional Testing: Ensure doors, drawers, and other elements operate smoothly.
07
Final Inspection and Cleanup
-
Client Walkthrough: Review the installation with the client to ensure satisfaction. Address any concerns or adjustments.
-
Cleanup: Remove debris, tools, and packaging materials. Leave the space clean and ready for use.
08
Follow-Up and Support
-
Client Education: Provide maintenance tips and recommendations for longevity.
-
Warranty Service: Discuss warranty terms and any future support options.
-
Feedback Request: Collect client feedback to improve services.
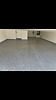
Sunset Customz Process

Concrete Coatings Workflow Process:
-
Initial Assessment
-
Surface Preparation
-
Priming
-
Base Coat Application
-
Decorative Layer (Optional)
-
Topcoat Application
-
Quality Inspection
-
Cleanup
-
Final Walkthrough
-
Follow-Up
Custom Cabinets Workflow Process:
-
Initial Consultation
-
Design Phase
-
Quote and Contract
-
Material Procurement
-
Manufacturing/Pre-Installation
-
Installation
-
Cleanup
-
Final Inspection
-
Follow-Up and Support